AI Predictive Maintenance: Cutting Downtime by 15% in US Factories by 2025
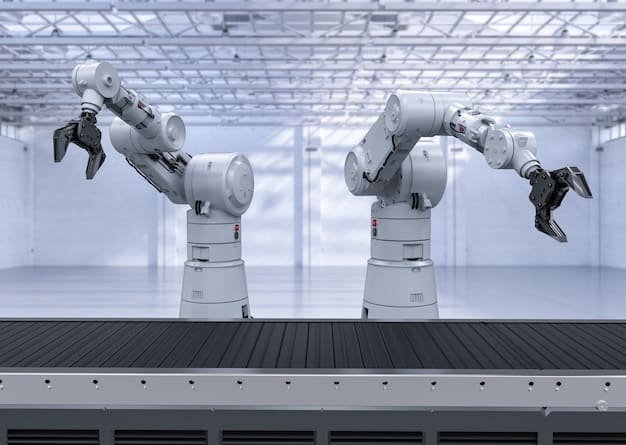
AI-powered predictive maintenance is poised to revolutionize US manufacturing by 2025, potentially reducing equipment downtime by 15% through advanced data analysis and proactive maintenance strategies, leading to increased efficiency and cost savings.
Imagine a future where factories in the US experience significantly less downtime, thanks to the power of artificial intelligence. This is not a distant dream, but a rapidly approaching reality. AI-powered predictive maintenance is set to transform the manufacturing landscape, offering the potential to cut equipment downtime by 15% by 2025.
The Rise of AI in Predictive Maintenance
Predictive maintenance, powered by artificial intelligence, is rapidly changing how US manufacturers approach equipment upkeep. This shift is driven by the increasing availability of data and advancements in AI algorithms, enabling more accurate predictions of equipment failures and optimizing maintenance schedules.
Understanding Traditional Maintenance vs. Predictive Maintenance
Traditional maintenance strategies often fall into two categories: reactive maintenance, which involves fixing equipment after it breaks down, and preventative maintenance, which relies on scheduled maintenance based on time intervals or usage. Both approaches have limitations.
- Reactive maintenance can lead to unexpected downtime, disrupting production schedules and increasing costs.
- Preventative maintenance can result in unnecessary maintenance, wasting resources and potentially causing damage to equipment.
- Predictive maintenance, on the other hand, uses data analysis and machine learning to predict when equipment is likely to fail, allowing maintenance to be performed only when needed.
This proactive approach minimizes downtime, reduces maintenance costs, and extends the lifespan of equipment.
How AI Enhances Predictive Maintenance
AI algorithms can analyze vast amounts of data from various sources, including sensors, historical maintenance records, and environmental conditions, to identify patterns and predict equipment failures with greater accuracy than traditional methods. This capability is crucial for achieving significant reductions in downtime.
In essence, AI transforms predictive maintenance from a reactive approach to a proactive one, allowing manufacturers to anticipate and address potential problems before they escalate into costly breakdowns.
The adoption of AI in predictive maintenance represents a significant step forward for US manufacturing, enabling companies to operate more efficiently, reduce costs, and improve overall productivity.
Key Components of AI-Powered Predictive Maintenance Systems
Implementing an effective AI-powered predictive maintenance system involves several key components working together seamlessly. These components include data collection, data analysis, machine learning algorithms, and a user-friendly interface for maintenance personnel.
Data Collection and Sensors
The foundation of any AI-powered predictive maintenance system is the collection of data from equipment. This data is typically gathered using a variety of sensors that monitor different aspects of equipment performance, such as temperature, vibration, pressure, and oil analysis.
These sensors provide a continuous stream of data that can be analyzed to detect anomalies and predict potential failures. The quality and quantity of data are critical to the accuracy of the AI algorithms.
Data Analysis and Machine Learning Algorithms
Once data is collected, it is analyzed using machine learning algorithms to identify patterns and predict when equipment is likely to fail. These algorithms can be trained on historical maintenance data and real-time sensor data to continuously improve their accuracy.
- Supervised learning algorithms can be used to predict failures based on labeled data, such as historical maintenance records.
- Unsupervised learning algorithms can be used to identify anomalies and patterns in the data without labeled data.
- Reinforcement learning algorithms can be used to optimize maintenance schedules based on feedback from the system.
The choice of algorithm depends on the specific application and the available data.
By leveraging these key components, manufacturers can create a predictive maintenance system that accurately predicts equipment failures, optimizes maintenance schedules, and reduces downtime.
The integration of these components requires careful planning and execution, but the potential benefits are significant.
Benefits of Reducing Downtime in US Manufacturing
Reducing downtime in US manufacturing offers a multitude of benefits, ranging from increased productivity and cost savings to improved safety and enhanced competitiveness. The impact of downtime on manufacturing operations can be significant, making it a critical area for improvement.
Increased Productivity and Output
One of the most direct benefits of reducing downtime is increased productivity and output. When equipment is running smoothly and reliably, manufacturers can produce more goods in less time, leading to higher revenues and profits.
AI-powered predictive maintenance helps to minimize unexpected downtime, ensuring that production schedules are maintained and output is maximized.
Cost Savings and Efficiency
Downtime can be costly for manufacturers, both in terms of lost production and the expense of emergency repairs. AI-powered predictive maintenance can help to reduce these costs by identifying potential problems before they lead to breakdowns.
This proactive approach allows manufacturers to schedule maintenance during planned downtime, minimizing disruption to production and reducing the need for costly emergency repairs. Additionally, predictive maintenance can help to optimize maintenance schedules, reducing unnecessary maintenance and saving resources.
Improved Safety and Reduced Risk
Equipment failures can pose safety risks to workers, especially in industries such as manufacturing where heavy machinery is involved. AI-powered predictive maintenance can help to improve safety by identifying potential hazards before they lead to accidents.
- By predicting equipment failures, manufacturers can take proactive steps to address safety concerns, such as repairing or replacing faulty equipment.
- Regular maintenance and inspections can help to identify and correct potential safety hazards before they cause accidents.
- Creating a culture of safety through training, communication, and employee involvement can help to prevent accidents and injuries.
This can lead to a safer working environment and reduce the risk of accidents and injuries.
Reducing downtime offers a wide range of benefits for US manufacturing, making it a critical area for improvement.
Challenges and Considerations for Implementation
While the benefits of AI-powered predictive maintenance are clear, implementing such a system can be challenging. Manufacturers need to consider various factors, including data availability, integration with existing systems, and the need for skilled personnel.
Data Availability and Quality
One of the biggest challenges in implementing AI-powered predictive maintenance is the availability and quality of data. AI algorithms require large amounts of data to train effectively, and the data must be accurate and reliable.
Manufacturers may need to invest in sensors and data collection systems to gather the necessary data. They also need to ensure that the data is properly cleaned and processed before it is used to train the AI algorithms.
Integration with Existing Systems
Integrating an AI-powered predictive maintenance system with existing systems can also be challenging. Manufacturers may need to integrate the system with their enterprise resource planning (ERP) system, manufacturing execution system (MES), and other systems.
Skills and Expertise Required
Implementing and maintaining an AI-powered predictive maintenance system requires specialized skills and expertise. Manufacturers may need to hire data scientists, machine learning engineers, and other professionals with the necessary skills.
Manufacturers without the necessary skills in-house may need to partner with external consultants or vendors to help them implement and maintain the system.
Case Studies: Successful AI Predictive Maintenance Implementation
Examining real-world examples of successful AI-powered predictive maintenance implementation can provide valuable insights for US manufacturers considering adopting this technology. These case studies demonstrate the potential benefits and highlight the key factors for success.
Case Study 1: Automotive Manufacturer
A leading automotive manufacturer implemented an AI-powered predictive maintenance system to monitor the performance of its production line equipment. The system used sensors to collect data on temperature, vibration, and other parameters, which was then analyzed by machine learning algorithms to predict equipment failures.
- The system helped to reduce downtime by 15%, resulting in increased productivity and cost savings.
- The manufacturer also saw a significant improvement in equipment lifespan and a reduction in maintenance costs.
- The success of this implementation was attributed to the manufacturer’s commitment to data quality, integration with existing systems, and investment in skilled personnel.
Case Study 2: Chemical Processing Plant
A chemical processing plant implemented an AI-powered predictive maintenance system to monitor the performance of its pumps, valves, and other critical equipment. The system used data from sensors and historical maintenance records to predict equipment failures and optimize maintenance schedules.
By leveraging real-world examples, manufacturers can gain a better understanding of the potential benefits of AI-powered predictive maintenance and the key factors for successful implementation.
The Future of AI in US Manufacturing Maintenance
The future of AI in US manufacturing maintenance is bright, with continued advancements in technology and increasing adoption by manufacturers. As AI algorithms become more sophisticated and data becomes more readily available, the potential benefits of AI-powered predictive maintenance will continue to grow.
Continued advancements in AI Algorithms
AI algorithms are constantly evolving, with new techniques and approaches being developed all the time. These advancements are leading to more accurate predictions of equipment failures and more effective maintenance strategies.
As AI algorithms become more sophisticated, they will be able to analyze data from a wider range of sources and identify more subtle patterns that can indicate potential problems.
Increasing Adoption by Manufacturers
As manufacturers become more aware of the benefits of AI-powered predictive maintenance, adoption rates are expected to increase. This trend will be driven by the need to improve efficiency, reduce costs, and enhance competitiveness.
As more manufacturers adopt AI-powered predictive maintenance, the technology will become more widely available and affordable, making it accessible to smaller businesses.
Integration with IoT Devices
The Internet of Things (IoT) is playing an increasingly important role in manufacturing, with more and more devices being connected to the internet. This connectivity is enabling manufacturers to collect vast amounts of data from their equipment, which can then be used to train AI algorithms.
One day, manufacturing processes will be streamlined further and improved through predictive analysis.
Key Point | Brief Description |
---|---|
⚙️ AI Predictive Maintenance | Uses AI to predict equipment failures, reducing downtime. |
📊 Data Collection | Sensors monitor equipment, providing data for analysis. |
💰 Cost Savings | Reduces downtime and maintenance costs, improving efficiency. |
🏭 US Manufacturing | Aims to cut equipment downtime by 15% by 2025. |
Frequently Asked Questions
▼
AI-powered predictive maintenance uses artificial intelligence to analyze data from sensors and other sources to predict equipment failures and optimize maintenance schedules.
▼
AI algorithms can identify patterns and anomalies in data that indicate potential equipment failures, allowing maintenance to be performed before breakdowns occur, minimizing downtime.
▼
Benefits include increased productivity, reduced maintenance costs, improved safety, and extended equipment lifespan. It also enhances overall operational efficiency.
▼
Data from sensors, historical maintenance records, and environmental conditions are essential for training AI algorithms and predicting equipment failures accurately and promptly.
▼
Challenges include data availability, integration with existing systems, and the need for skilled personnel to manage and maintain the AI systems effectively.
Conclusion
In conclusion, AI-powered predictive maintenance offers a transformative opportunity for US manufacturing to achieve significant reductions in equipment downtime by 2025. While challenges exist, the potential benefits of increased productivity, cost savings, and improved safety make it a worthwhile investment for manufacturers looking to stay competitive in the modern era.